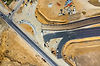
Services > Site Services
Site Services
Further to our commitment to our customers for a complete life cycle support of our products PulseTech offers an experienced team of specialists to who provide on site support for electrical drive systems such as MV variable speed drives, soft starters, liquid resistance starters, and static excitation control systems.

Commissioning
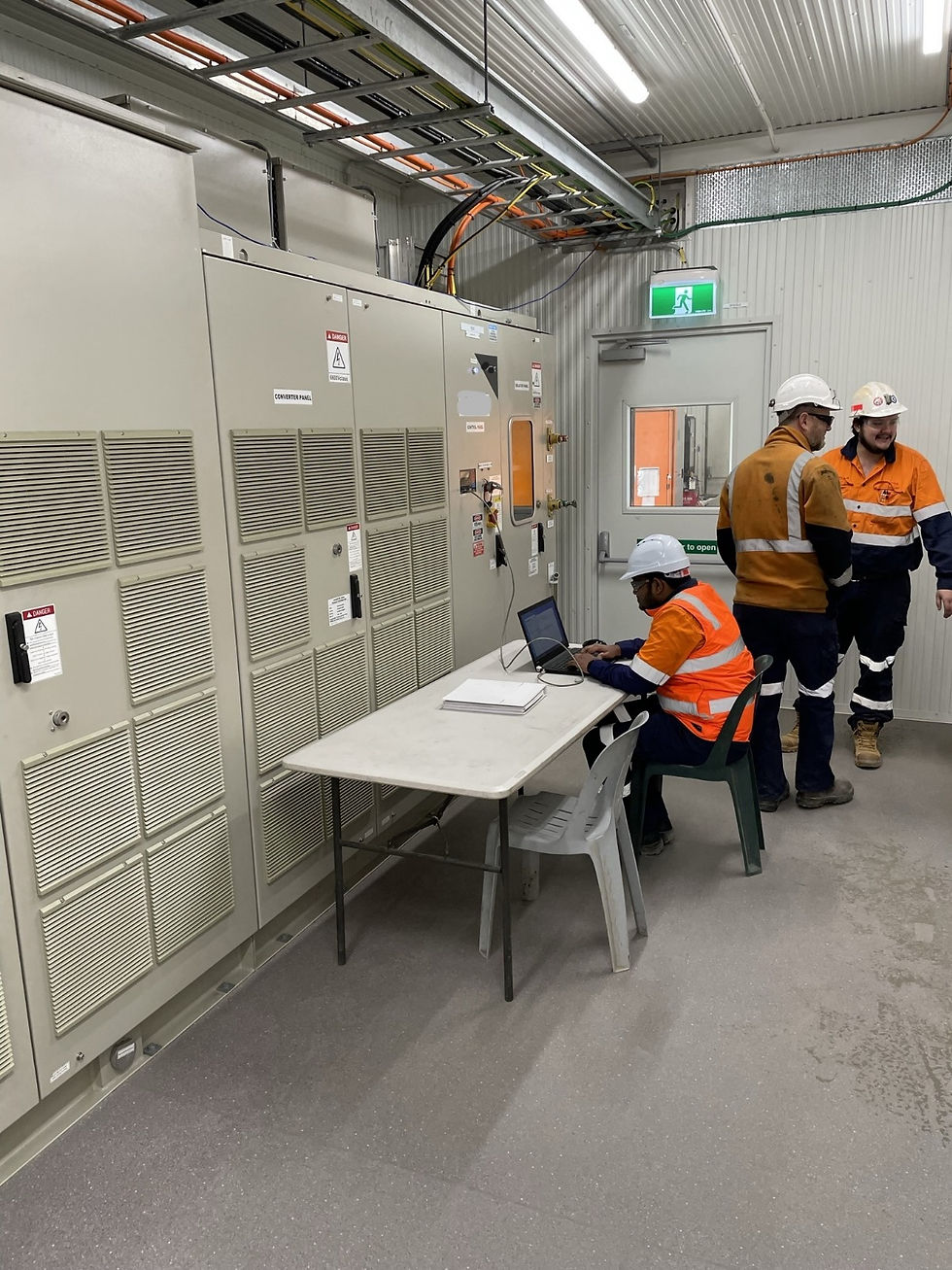.jpeg)
Commissioning is a crucial stage of a project, and its execution often defines the success of a project. It must be performed safely, within time constraints, in accordance with design specifications and result in reliable long-term operation of plant and equipment.
As specialists in installation supervision and commissioning of liquid resistance starters, electrical drives and systems, our team consists of highly experienced engineers that can assist with the successful commissioning of your plant and equipment.
Our primary goal is when commissioning is to achieve safe, flawless start up and perform by focusing on diligent preparation, planning, and applying solid risk management processes and controls.
PulseTech commissioning activities include:
-
validation of installation works ensuring compliance to Australian standards and manufacturer’s requirements
-
verification of factory settings of the equipment
-
settings adjustments to meet plant requirements or project control philosophy
-
functional testing
-
equipment first energisation and no-load testing
-
equipment tuning according to the load requirements to ensure long-term trouble-free operation
This last step is often overlooked as soon as the equipment is started up and handed over to operations, only to result in nuisance tripping sometime in the future. Upon completion of commissioning, a comprehensive commissioning report is issued for the customer’s record keeping.
Preventative maintenance is key in maintaining reliability and minimising likelihood of unscheduled downtime and lost production due to equipment failure. We have the knowledge, experience, and manufacturer-backed procedures to ensure your equipment is maintained to the highest standards.
PulseTech maintenance activities include:
-
verification that the equipment is maintained in accordance with the manufacturer’s requirements
-
recording or capturing of equipment operational performance data
-
inspection of individual components ensuring they are in acceptable conditions
-
cleaning, parts replacement, or adjustments to restore equipment to optimum levels
-
review and analysis of equipment fault history and historical performance data
Finally, the equipment is operated (subject to operational readiness) with all key variables monitored to ensure trouble free operation prior to our departure from site.
As an additional risk management strategy on behalf of our clients, a spare parts audit is conducted whilst on site ensuring that the correct parts are available, in good condition and adequate quantities are kept in stock. Upon completion of the work, a comprehensive service report is issued for the customer’s record keeping.
.jpeg)
Preventative Maintenance
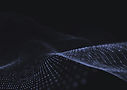
Enquiry Form
Have an immediate enquiry? Please leave your details below and we will get in touch shortly.